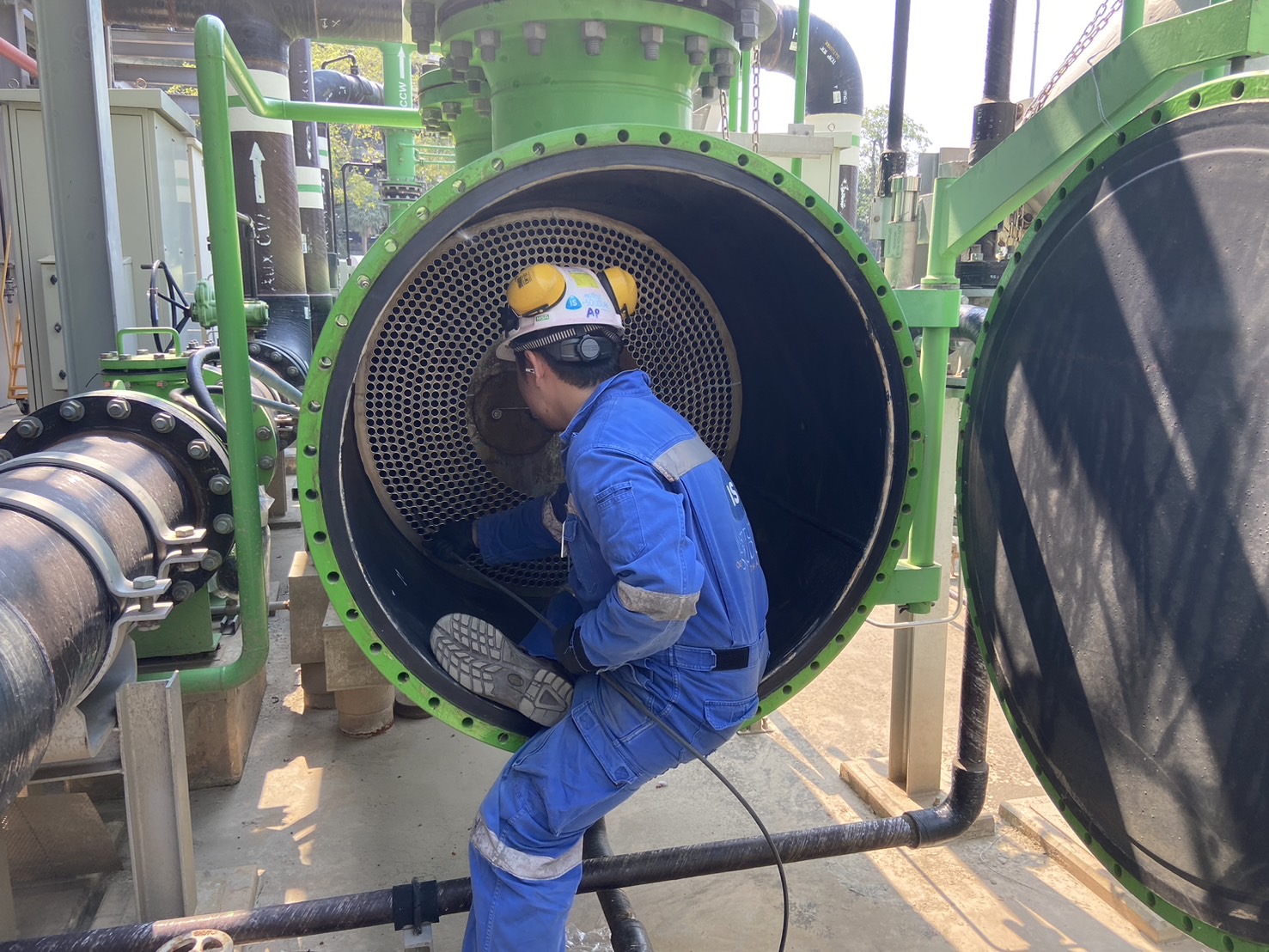
Eddy current testing (ECT) is a non-destructive testing (NDT) technique used to inspect and evaluate the integrity of conductive materials for various purposes, including flaw detection, material characterization, and quality control.
It relies on the principle of electromagnetic induction and the generation of eddy currents in the material being tested.
Eddy current testing is particularly useful for detecting surface and near-surface defects, as well as measuring the thickness of conductive coatings.
Remote field testing (RFT) is a non-destructive testing (NDT) technique used for inspecting ferromagnetic tubular structures, such as pipelines and heat exchanger tubes.
It is primarily employed to detect and assess flaws, corrosion, and other defects in the walls of these tubes without the need for direct contact with the interior surface of the tube.
RFT is particularly useful in industries like oil and gas, petrochemical, and power generation, where the integrity of such tubular structures is critical.
Near field testing (NFT) is a non-destructive testing (NDT) technique used for inspecting and evaluating materials, components, or structures, particularly in applications where close proximity to the test object is required.
Unlike some other NDT methods that rely on the propagation of waves over long distances, NFT operates in the near field region, which is close to the surface of the material or structure being tested.
This technique is often employed to detect and assess defects, discontinuities, or other anomalies in materials and components. Near field testing can be applied to various materials, including metals, composites, and concrete.
Magnetic Flux Leakage (MFL) is a non-destructive testing (NDT) technique used for inspecting and assessing the integrity of ferromagnetic materials and structures.
It is commonly employed to detect and locate defects such as corrosion, wall-thinning, and other anomalies in pipelines, storage tanks, and other structures made of materials like steel.
MFL relies on the principles of magnetism and electromagnetic induction to perform inspections.
The Internal Rotary Inspection System (IRIS) is a non-destructive testing (NDT) technique used for inspecting the integrity and condition of tubes, pipes, and heat exchanger tubes, particularly those used in industries such as power generation, petrochemical, and oil and gas.
IRIS is specifically designed for assessing the internal surface of tubular structures and detecting defects such as corrosion, wall-thinning, pitting, and cracking.
777/32 Moo 9 Bang Pla Sub-district
Bang Phli District , Samut Prakan 10540
Thailand
131/52 Moo 2 Plernjai 4 Village,
Tubma Sub-district, Muangrayong District,
Rayong 21000
Thailand